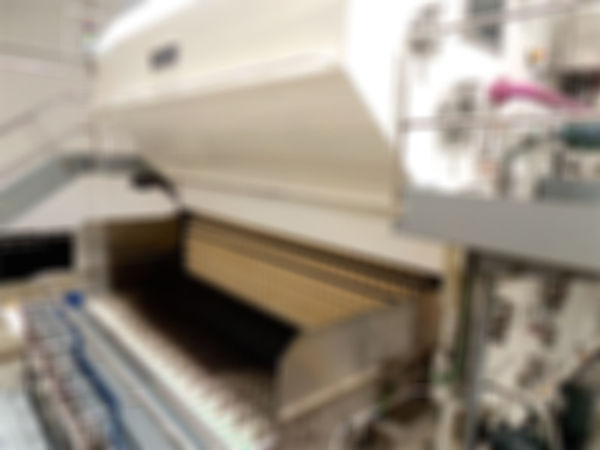
Equipment for Bottling Lines
With its own technology that incorporates global engineering trends, the company has conquered its space as a traditional supplier of Bottle Washers and Tunnel Pasteurizers in the national market. Efficient after-sales work guarantees the durability of products, through periodic upgrades, generating updated solutions with high performance and low operating costs.
Liess Bottle Washers and Pasteurizers are characterized by having the lowest water and energy consumption in this segment, as a result of constant technological development and innovative processes.
Lavadoras de Garrafas Ecoline
Designed to optimize the entire bottle washing and rinsing process.
• Automation aimed at total control of the process and reduction of consumption, with complete recipes for each type of bottle.
• Drives with electronic synchronism, without mechanical transmission elements.
• Unloading system and loading table with orbital system, with electronic synchronization and setup according to pre-established recipes.
• Control of tank levels, detergent concentration and automatic tank temperatures.
• Configurations with or without label extractors.
• Plastic bottle holder cells in sizes 82 mm, 95 mm, 105 mm, 125 mm and 150 mm, serving a wide variety of bottles.
Por que incluir a lavadora de garrafas Ecoline
em sua linha de produção?
-
EcoLine washers were developed with a modular design, meeting the strictest needs of modern bottling lines, both for glass bottles for beer and soft drinks, as well as RefPet bottles, labeled or not.
The wide variety of configurations allows working with bottles with diameters from 50 mm (200 ml) to 120 mm (3.0 liters RefPet), with heights of up to 380 mm.
There will always be a washing machine model to meet your needs, both in terms of production requirements and automation and accessory configurations.
Ecoline is the best alternative:
• Reduction of 8% to 10% in steam consumption;
• Total water consumption: 0.18L/bottle washed;
• Water savings of more than 50% compared to traditional systems.
RESULT: More efficiency with low water and energy consumption.
Sistema regenerativo de água e energia
PRE-WASH AREA:
Pre-washing and preheating with three stages, one for immersion;
• Greater regeneration of energy recovered from rinsing areas;
• Removal of broken glass and straws;
• Self-cleaning and self-purging sludge sieve;
• Less contamination of the caustic solution;
• Longer useful life of the caustic solution and additives.
RINSE ZONE:
Pre-rinse with five stages;
• Greater efficiency in rinsing and removing heat from combs and bottles;
• Lower water consumption for rinsing and cooling bottles;
• Control of tank levels using recovered water;
• Control panel with defined positions for operation and maintenance;
• Dynamic water flow and pressure control process according to each recipe.
One Way Flow Pasteurizer
The Pasteurizer is not just a production machine, its main function is to guarantee the beer pasteurization process. Liess has excellence in the brewing method and has decades of experience in machine building. The result of this is a line of Pasteurizers that responds to high levels of production efficiency and, above all, guarantees the final quality of the product, providing a long life and preserving the unparalleled flavor of a good beer.

The One Way Flow Pasteurizer line provides the most advanced tunnel pasteurization technology. The main feature of this model is total control of the pasteurization process in real time, with multiple heating and cooling zones with fluctuating temperatures, depending on the number of UPs (Pasteurization Units) acquired by bottles or cans at each stage of the cycle. . The machine guarantees the specified range of UPs in normal operating conditions, in line stoppages and at the end of production. These phases cause imbalances that are corrected by the intelligent control system.
To allow rapid changes in required temperatures without causing spikes in water and energy consumption, the equipment has cold, hot and warm water tanks, which act as thermal lungs and supply stored heat and cold quickly and economically. The procedure
regenerative energy system, together with a cooling tower, guarantees operation with low overall energy and water consumption.
The construction is entirely made of stainless steel, modular and without internal elements that require frequent maintenance. The container conveyor belt can be plastic or stainless steel, depending on the customer's specifications. The pumps are protected by an automatic waste filtration belt, minimizing the need to clean the nozzles.
The operation is entirely automatic, with full control over all variables and a user-friendly interface for the operator.
CIP Central for Bottling Line

As a process specialist, Liess supplies a wide range of CIP Plants for Bottling Lines. The project can be configured according to particular needs, from the simplest manual operation to the most complex, fully automatic.
CIP Liess Plants can be produced with two, three, four or more tanks, as well as serving one or more lines or equipment simultaneously. The volume of the tanks, CIP flow and pump pressure also comply with the specifications of each demand. With this flexibility, there will always be an ideal center for different applications.